Vendor Shipping Guidelines
Freight Appointments
OpenDock Carrier Training Document
Please schedule your inbound freight appointments via Opendock | Dock Scheduling Software. Please reference the Open Dock Carrier training document.
ISLD thoroughly reviews and approves loads scheduled on Open Dock. Scheduled loads are required to have an accurate bill of lading (BOL) with item description and NABCA numbers. A finalized BOL is required 14 days from the scheduled arrival date. ISLD will review loads scheduled in Open Dock for compliance and our team will approve the appointment two weeks prior to the shipment delivery date. If the load is tagged “Not Approved”, you are expected to modify the load and upload a new BOL/Packing Slip to the appointment on Open Dock. If the load is tagged “Not Approved”, we will send an email communication to the supplier, broker & the contact included on the Open Dock freight appointment.
If this load is not updated by 14 days prior to the arrival date, the supplier runs the risk of losing the appointment slot or rejection of the entire or partial load when freight arrives at the distribution center.
It is imperative that you are reviewing your current weeks on hand in the Supplier/Broker Portal to build your loads. If you do not currently have access, your broker can provide this to you. The portal weeks on hand value is calculated based on depletions in a rolling 12 month period and entered under the “Warehouse Weeks on Hand” column. This total includes both Bailment and Corporate inventory in the warehouse and all items are color coded based on the warehouse inventory levels available in our facility. Items over 8 weeks of inventory are considered overstock and highlighted in blue and inventory levels should be maintained between 4-8 weeks consistently. Loads will not be approved if the amount of inventory pending puts inventory levels over 8 weeks.
Pallet Standards
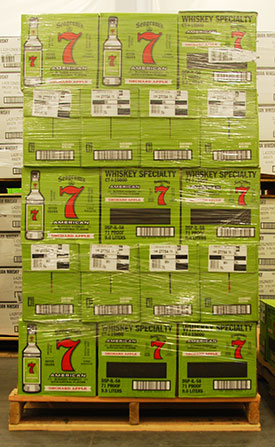
Please note: Slip Sheet deliveries will no longer be accepted at the ISLD warehouse. ISLD will provide a 60-day grace period for those currently shipping in slip sheets to comply. Items not in compliance will be subject to delisting should there be multiple violations of this requirement.
All Inbound Freight deliveries must have a standard GMA 40” x 48” pallet and must be Grade A or Grade B for all items delivering on that shipment. All In-bound pallets must be stretch wrapped.
The Idaho State Liquor Division (ISLD) uses the Automated Storage and Retrieval System (ASRS).
The use of this automated equipment requires that every pallet being delivered to ISLD must comply with the following size standards. These standards will be automatically verified on every pallet entering the ASRS:
- Maximum Pallet Height, including pallet: 72”
- Maximum Pallet Weight: 2,800 lbs
- Maximum Pallet Width: 42”
- Maximum Pallet Length: 48”
*Products may not arrive on slip sheets*
Non-Complying Pallets:
At its option ISLD may elect to do any of the following to bring pallet dimensions into compliance:
- Refuse to accept delivery until pallets are repackaged and compliant.
- Require Idaho Sales Representative or Designated Supplier/Broker to take possession of non-compliant pallets until items are repackaged and compliant.
- ISLD may restack or down-size pallets to bring pallets into compliance.
ISLD may restrict retail display activation and future listings of the Supplier’s items for any additional material handling that may be required by ISLD warehouse staff.
Special Order Shipping Guidelines
All Special Orders must arrive in products original case shipper, with correct labeling and not in a repacked case.
- This ensures all Special-Order items are received quickly, efficiently, and accurately into our system.
- Items arriving in repack boxes add receiving delays, increased labor and can lead to inventory discrepancies.
- Items not arriving in original case shipper face delays in processing and delisting if there are multiple violations of this requirement.
Case Code Label Instructions for Spirits
The “case code label” is one of the benefits to the control state coding system.
The following is a label example and explanation of the approved case code.
Example Label:
- Case code labels should be on white stock paper with black lettering unless approved otherwise.
• The size of the product must be included. - Product Description
- Control State Code Number
• “320” represents the three-digit prefix to further identify class and type.
• “43136” is the unique CSC number. (Note: All leading zeros should be omitted.)
• “75” represents the two-digit suffix identifying the size.
• The control state code number should be 7/8” to 1” high.
• The prefix and suffix number should be ¼” to ½” high. - Other State Code Numbers
• Pennsylvania and North Carolina code numbers should be 7/8” to 1” high. All other state code numbers should be ½” high. - UPC Symbology
• The UPC Symbology should be located in the lower left hand corner of the case code label. - Location
• The label should be located on an end panel.
Please note, all products are required to be shipped in their original shipper/boxes and not shipped in a repack box. This ensures all items are received correctly under the right item code and processed quickly into inventory. Items arriving in repack boxes add receiving delays and can cause inventory discrepancies.
All bar codes (UPC, EAN, SCC-14, SSCC-18, and other Als and Data) shall be printed and placed in a vertical bar configuration (picket fence). Placement of bar codes is independent of print technology and Symbology employed.
Case Code Label Instructions for Related Beverage Products
The “case code label” is one of the benefits to the control state coding system.
The following is a label example and explanation of the approved case code.
Example Label:
- Case code labels should be on white stock paper with black lettering unless approved otherwise.
• The size of the product must be included. - Product Description
- Control State Code Number
• “398” represents the three-digit prefix to further identify class and type.
• “62634” is the unique CSC number. (Note: All leading zeros should be omitted.)
• “35” represents the two-digit suffix identifying the size. - UPC Symbology
• A scannable UPC Symbol must be included on the case code label. - Location
• The label should be located on an end panel.
All bar codes (UPC, EAN, SCC-14, SSCC-18, and other Als and Data) shall be printed and placed in a vertical bar configuration (picket fence). Placement of bar codes is independent of print technology and Symbology employed.
Revised August 2023